Density 40/175 gr/m2 .
Width– 1575 mm, copper net width 1950 mm.
Productivity 8 -10 tons/shift (10 hrs)
Raw materials - any waste paper
Desing whiteness is not lower than 90 % special technology affords whiteness of 95%
Water consumption 50 tonn/1 ton of paper
Electric power consumption - 400 kW
Including:
Pulping 300 kW
Main unit 70 kW
Winding and cutting 25 kW
Required heat for drying drums - 2 tons/hr
Steam of medium saturation : 0.3 Mpa.
Steam temp at outlet 900 C
Weight : main unit – 50 tons, whole line – 60 tons.
Main unit's size: 4870mm*21000mm*5630mm
Number of workers: 10 persons/shift , 3 shifts.
Working day – 22,5 hrs.
Production area: 650 m2
Productivity: 10 tons/day
Time of manufacturing - 3 months
Manufacturing : The factory is divided into 3 sections
1.Pulp production
At this section the waste paper is loaded into special tanks where it is soaked in large amount of water with constant stirring.
For crushing large pieces vibration screen and wiping are used, then the metals (such as staples) are removed from the resultant mixture, followed by washing and pumping out the sand.
As the waste paper is stored on the ground or, at the best, under awning, it is usually is greatly soiled by sand, ground, petty stones. Then the resultant mixture is treated with washing chemical reagents and bleachers.
It is necessary to remove paints, fats, organic remains and dyers from the pulp. Then when the waste paper turned into honogeneous bleached substance without alien admixtures it is necessary to remove excessive water from the mixture and beat it up. The resultant substance is called pulp
Pulp section consists of two parts :
First part - tanks, pools and fluid reservoirs .
Second part - attached implements for tanks - pumps, electric engine, stirrers etc
Vacuum pump, model 13 – 1 unit.
Suction box – 3 units.
Rinsing machine (35m3) – 2 units.
Pulper (8m3) – 1 unit.
Vibration screen (1.8 m3) – 1 unit.
Twin-disk refiner -380 – 2 units.
Pusher (diameter 700) – 4 units.
Pulp pump –100 – 6 units.
Pulp pump –150 – 4 units
Slime and sand pump IS200—150 – 1 unit.
Sand box -606 – 1 unit.
Reagent tanks 4 units
Submersible attached stirring systems - 2 units
Sterilizer - 1 unit
2.Paper production
The pulp is fed to paper-making machine There two netter drums they draw pulp, thick fraction sediments on the net whereas excessive water leaves the mixture through the net. Thick pulp fraction runs via aligning rollers, the slab is shaped to the required thickness and is aligned over the whole area of the future sheet.
When the pulp has required shaped and thickness and the water is removed, the band enters the baking drum, where the water is completely removed, the band is dried and stick into homogeneous mass, thus turning into paper.
Double roll paper-making machine – 1 unit.
Net socket (2 units.), diameter 1500 mm*2100 mm, Coach (3 units.), diameter 400*2200 mm, Rubber HS - 380±2,
pressure making pneumatic plant
Shape generatin netter plant – 1 unit.
stone shaft (1 unit.), diameter 550*2100 mm
rubber roller (1 unit.), diameter 500*2100 mm, Rubber HS 900±2, pressure making pneumatic plant
Drying drum with vent cap -1 unit
Drying section: Drying drum (2 units.), diameter 2500*1950 m
2 rubber rolls, diameter 500*2100 mm, Rubber HS is 900 т 900±22
pressure making pneumatic plant, fan -1 unit
Main machine
Finished paper weight 45-60 gr/m2
Paper width: 1760 mm
Copper wire width : 2100 mm
WIdth between drum holding posts: 2600 mm
Power-416kW
Height -4500 mm
Lenght -30 000 mm
Width -2800 mm
Workers - 8 persons/shift, 3 shifts
Operating area - 500 m2
Productivity/shift - 10 tons/day
Operating parameters - (premises)
Drive and control - variable frequency speed control, step gearing, closed circuit control system.
Time of manufacturing - 2 months
3. Winding, re-winding, cutting
Paper production is a continuous process and the sheet made by paper-making machine has length of several kilometers
It produces 120 000 meters/8hrs During the production the paper is wound on the coil. Its diameter can reach 2-3 meters, weight- 9-10 tons.
Such size of coil makes difficult its transportation, that's why there's rewinding and cutting section in the shop.
For this purpose section № 3 was built .The paper is wound from the large coil to standard small coils.
Their weight varies from 300 to 500 kg., diameter 650-800 mm. The line also includes cutting machine that cuts the paper according to the set parameters.
The coil of weight of 300 kg and diameter less than 100 mm is cosidered the product ready for sale.
Rolling section : 3-rolls glazer (1760 mm)
barrel-like reeling machine (1760 mm)
Glazer (1760 mm) – 1 unit.
Reeling machine (1760 mm) – 1unit.
Winding machine (1760 mm) – 1 unit.
The set doesn;t include:
boiler
coarse cloth net
two open concrete tanks
cartridge making machine
mounting cable
Mounting pipe
Mounting stop valves (in-out)
Supplementary equipment
Sometimes such production lines are supplemented by machine for making cardboard cartriges used to wind paper on them
Standard cutting of paper is perfomed on special equipment in special shops and factories.
First the paper is unwound, during unwinding it is cuts into sheets of 3-5 m2 the latter are piled by 500 sheets, the resultant sheets are cut into set standard sizes using guillotine shears.
In production of high-grade paper dust and cuts should be removed.
The paper bundles are packed in brand-named packages or wrapped into a large piece of the same paper and corded
THis set doesn't include the equipment for producing paper of standard size .
Flowchart:
1
Waste paper→ Pulper→ vibration screen→ pulp reservoir →pulp pump→ screen→ refiner→ thickener→ pulp reservoir → pulp pump → sand pump→ rinsing reservoir → pulp reservoir → pulp pump →pulp reservoir →pulp pump→
2
Paper-making machine →
3
Rolling machine → winding machine → cutting machine → finished product
Photo of the equipment:
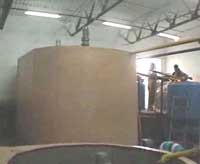
Pulper

Pulper
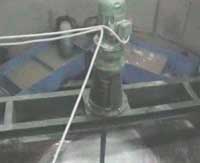
Attached submersible equipment in open rinsing pools

Submersed part of the attached equipment
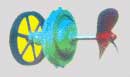
Submersible attached equipment
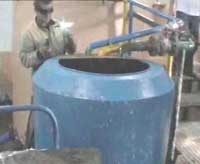
Refiner
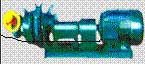
Mounting of refiners
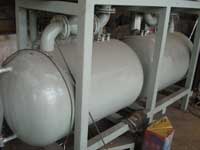
Pools for chemical reagents for refinement of pulp
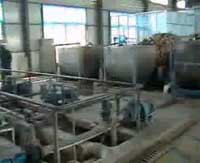
Pulp pump
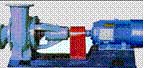

Assembled pulp shop
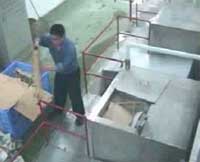
Loading of waste paper
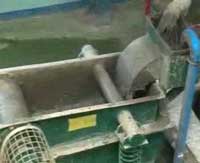
Screen
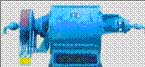
Thickener
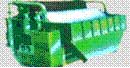
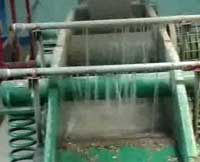
Sand pump
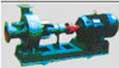
Sand and metal catcher
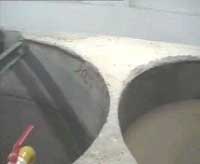
Recommended layout for open pools
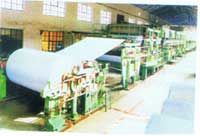
Paper-making making and finished paper receiving machine
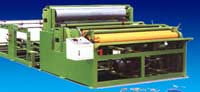
Winding machine
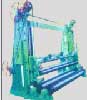
Rolling machine
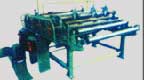
Winding and cutting machine (diameter 1800mm, 2600mm, 3400mm)
Paper, density 40-120 gr/m
Weight 4-8T/D, width up to 2400 mm